View & download of more than 204 Kipor PDF user manuals, service manuals, operating guides. Inverter, Portable Generator user manuals, operating guides & specifications. Kipor diesel-gen-service manual 1. Diesel generator single-phase: k de2200x/e k de3500x/e/t k de5000x/e/t k de6500x/e/t/ta k de6700t/ta k da6700ta/tao three-phase: k de6500x3/e3/t3 k de6700t3/ta3 k da6700ta3/tao3 maintenance manual 2.
KIPOR has the right generator to meet your power needs.
KIPOR – the best choice in portable power.

Outstanding serviceability and reliable performance in a simple, easy-to-use design to make Kipor generators the best choice in portable power. Ideal for RV, Camping, Home Applications and many more.
Kipor Digital Sinemaster Generators provide clean and quiet portable power. These compact and lightweight generators are the perfect match for all your requirements, when you want all the conveniences at home, worksite or for leisure. The pure sinewave generators can run sensitive electronic equipment.
Kipor digital generators offer a much smaller and quieter form of portable power compared with traditional generators.
If you are looking for a generator that is compact, powerfull and quiet then Kipor generators are the optimum choice for you and value for money. Kipor Generators give you a saving of about 50% in size / weight.
Every Kipor generator has passed the EPA phase II standards and is CE certified. and Kipor itself is ISO9001 certified
Kipor Generators compact and lightweight design allows true portability of power for in the motorhome, caravan or boat.
Kipor digital generators offer the same sort of performance and quiet performance normally offered at 2-3 times the price from other well known industry generator manufacturers.

High quality power output is achieved with Kipor Generators by a built-in pure sine wave inverter, which filters the initial power of the alternator to minimise wave distortion and voltage fluctuation. This results in the output being more refined, clean and smooth. The inverter delivers a true Sine wave, no power spikes, surges or fluctuations of voltage, making it suitable for highly sensitive electronic equipment such as computers and laptops.
Kipor Generators are designed to meet strict environmental standards, Kipor digital generators provide environmentally friendly green power for use when out and about in your motorhome, caravan or out on the ocean wave.
Fuel economy is also at a premium with Kipor generatos, with fuel consumption (20 - 40 per cent lower than a traditional generator set under normal usage).
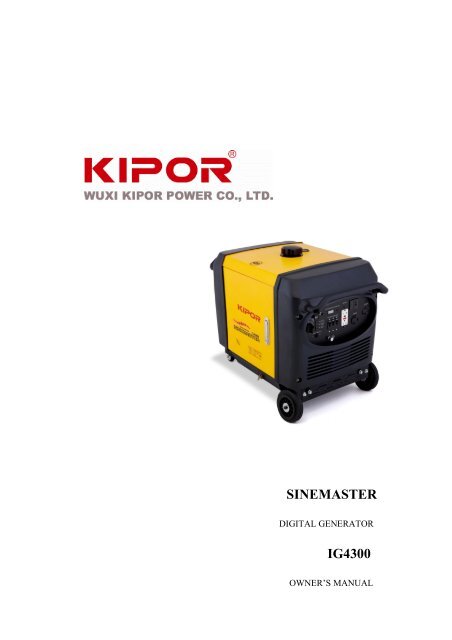
Kipor Generator Manual
A load-dependent smart throttle system automatically maintains engine speed and power output at the most efficient level under all usage loads, resulting in reduced fuel consumption, noise and vibration.
Kipor Generator Manual
All Kipor Power generators offer an approximate continuous runtime based on their full rated output.
KDE5000E KDE5000TA
The Coast Distribution System, Inc. January, 2007
PREFACE This manual covers the construction, function and servicing procedure of the Kipor KDE5000E and KDE5000TA Coast Distribution model generators. This manual is principally concerned with the generator specifications, function, troubleshooting and repair. See the owner’s manual for the preventive maintenance schedule and instructions. There is a separate manual to cover overhaul, repair and troubleshooting of the KM186FA diesel engine. Careful observance of the instructions contained in this manual will result in safe and quality service work. All information, illustrations, directions and specifications included in this publication are based on the latest product information available at the time of approval for printing. KIPOR POWER CO., LTD, reserves the right to make changes without incurring any obligation whatever. No part of this publication may be reproduced without written permission.
2
TABLE OF CONTENTS 1. Specifications and Data 1.1 Specifications ....................................................................................................4 1.2 KDE5000E wiring diagram................................................................................5 1.3 KDE5000TA wiring diagram ............................................................................6 1.4 Component Identification- KDE5000E..............................................................7 1.5 Component Identification- KDE5000TA ..........................................................8 1.6 Control Panel- KDE5000E ..............................................................................9 1.7 Control Panel- KDE5000TA .............................................................................9 1.8 KDE5000TA Digital Display Panel ...................................................................10 1.9 Serial number and bar code location ..............................................................11 2. Service Information .....................................................................................................12 2.1 The importance of proper servicing .................................................................12 2.2 Important safety precautions.............................................................................12 2.3 Service rules ....................................................................................................12 2.4 Electrical precautions ......................................................................................13 2.5 Generator Service Standards............................................................................14 2.6 Fasteners and torque values ..........................................................................15 2.7 Digital panel protection values ........................................................................15 2.8 Troubleshooting ...............................................................................................15 3. Generator Repair..........................................................................................................23 3.1 Start switch ......................................................................................................23 3.2 Voltmeter .........................................................................................................24 3.3 Circuit breaker .................................................................................................24 3.4 Oil alert ..............................................................................................................25 3.5 Generator ........................................................................................................28 4. Electrical Component Illustrations................................................................................30 4.1 Receptacle wiring ............................................................................................30 4.2 AVR adjustment.................................................................................................31 4.3 Battery charge regulator ..................................................................................32 4.4 Current transformer...........................................................................................32 4.5 Rotor checking ................................................................................................34 4.6 Stator test points ..............................................................................................35 4.7 Main stator winding check.................................................................................36 4.8 Stator secondary and sampling winding check ...............................................37 4.9 Charge winding check .....................................................................................38 4.10 Carbon brush check........................................................................................38 5. KDE5000TA display panel ..........................................................................................39
3
1. SPECIFICATIONS AND DATA 1.1 Specifications
Model
KDE5000E
KDE5000TA
Rated frequency (Hz)
60
60
Rated power (kVA)
4.5
4.5
Rated voltage (ACV)
120/240
120/240
Rated current (ACV)
37.5/18.8
37.5/18.8
3600
3600
Item
Rated speed (rpm) Generating set
Phase
Single phase
Power factor
1.0
Excitation mode
Self excitation constant voltage (AVR)
DC output
12V/8.3A
AC Receptacles
2 120 15A, 1 30A Twistlock, 1 30A 120/240,
Structure mode
Open frame
Coupling method
Enclosed
Transmission rigid connection
Gross weight lbs. (kg) Overall dimensions LxWxH in (mm)
Model
209 (95)
376 (171)
28.3x19.4x25.6
36.6x20.3x29.7
(720x480x845)
(930x515x755)
KDE5000E
Item Model Type
KDE5000TA KM186FAG
4-stroke,
single-cylinder,
air-cooled,
injection diesel engine Max output (kW/rpm)
6.6
Bore x stroke in (mm)
3.4x2.8 (86x72)
Displacement in (L)
0.418
Engine
Cooling system
Forced air-cooled system
Lubricating system
Pressure splashing
Lube oil capacity qt. (L)
1.5 (1.65)
Starting system
Recoil/electric
Fuel
Electric Diesel
Fuel tank volume gal (L)
3.9 (15)
Run time at rated load- hrs
4.2 (16)
8
Low oil alarm system
8.5 included
4
direct
1-2 KDE5000E wiring diagram
5
1-3 KDE5000TA wiring diagram
6
1.4 Component Identification- KDE5000E
7
1.5 Component Identification KDE5000TA
8
1.6 Control panel- KDE5000E OIL ALERT WARNING LAMP
VOLTMETER
START
SWITCH
CIRCUIT BREAKERS
20AMP
120VAC
GROUNDING STUD DUPLEX
30 AMP 120VAC RECEPTACLE
30 AMP 120/240VAC RECEPTACLE
1.7 Control Panel KDE5000TA START
SWITCH
CIRCUIT BREAKERS
DISPLAY PANEL
20A 120VAC DUPLEX
RECEPTACLE
PANEL FUSE
GROUNDING STUD
30A 120VAC RECEPTACLE
RECEPTACLE
9
30A 120/240VAC
1.8 KDE5000TA Digital Display Panel
The panel is designed to give the operator precise information regarding generator operation and current loads. Additionally, should the generator experience a condition necessitating shutdown, a fault code appears on the screen. When running, the green “RUN” light should be illuminated. Press the function “FUNC” button to change the display. A green light should appear above the digital readout to indicate the current function. You have a choice of voltage (120 or 240), power (VA), Frequency (HZ), total runtime in hours, and starting battery voltage. Panel programming is explained in section 5.
10
1.9 Serial number and bar code identification and location The generator serial number identifies your particular unit and is important when ordering parts and accessories. The bar code is used by your dealer and Coast Distribution for warranty administration.
The serial number for the KDE5000TA is located on the air inlet plate to the left of the diesel injection pump.
The serial number for the KGE5000E can be found on a
stainless
steel
shroud
surrounding the alternator the right of the engine.
The bar code is found in three locations:
on the generator,
on the packing crate or carton, and on the inside cover of the operator’s manual.
11
2. SERVICE INFORMATION 2.1 The importance of proper servicing Proper servicing is essential to the safety of the operator and the reliability of the generator. Any error or oversight made by the technician while servicing can easily result in faulty operation and/or damage to the equipment or injury to the operator.
!
Warning
Improper servicing can cause an unsafe condition that can lead to serious injury or death. Follow the procedures and precautions in this shop manual carefully. Some of the most important precautions are stated below. 2.2 Important safety precautions Be sure you have a clear understanding of all basic shop safety practices and that you are wearing appropriate clothing and safety equipment. When performing maintenance or repairs, be especially careful of the following: • Read the instructions before you begin, and be sure you have the tools and skills required to perform the tasks safely. • Be sure that the engine is off before you begin any maintenance or repairs. This will reduce the possibility of several hazards: - Carbon monoxide poisoning from engine exhaust. - Burns from hot parts. - Injury from moving parts. • Do not run the engine unless the instructions tell you to do so. Keep your hands and clothing away from rotating parts. • To reduce the possibility of fire or explosion, exercise extreme caution when working around gasoline. Use only a nonflammable solvent, not gasoline, to clean parts. Keep cigarettes, sparks and flames away from all fuel-related parts. 2.3 Service rules • Use genuine KIPOR or KIPOR-recommended parts and lubricants or their equivalents. Parts that do not meet Kipor’s design specifications may damage the engine. • Use the special tools designed for the product. • Always install new gaskets, O-rings, etc. when reassembling components. • Clean parts in cleaning solvent upon disassembly. Lubricate any sliding surfaces before reassembly. After reassembly, check all parts for proper installation and operation. • Many screws used in this machine are self-tapping. Be aware that cross-threading or
12
over tightening these screws will strip the threads and ruin the hole. • Use only metric tools when servicing this engine. Metric bolts, nuts and screws are not interchangeable with non metric fasteners. The use of incorrect tools and fasteners will damage the engine. 2.4 Electrical precautions • Hold the connector body to disconnect the connector. Do not disconnect by pulling the wire harness. To disconnect the locking connector, be sure to unlock first, and then disconnect. • Check the connector terminals for bend, excessive extrusion, missing terminals, or other abnormalities before connecting the connector. • To connect, insert the connector as far as it goes. If the connector is a locking type, be sure that it is locked securely. • Check the connector cover for breakage and check whether the connector female terminal is not opened excessively. Then, connect the connector securely. Check the connector terminal for rust. Remove the rust using an emery paper or equivalent material before connecting the connector. • Set the harness clips in the specified places of the frame securely, and secure the wire harnesses. • Clamp the cables securely. • Clamp the wire harnesses securely so that they do not interfere with the rotating parts, moving parts and hot parts. • Route and connect the wire harnesses properly. Be sure that the harnesses are not slack, twisted or pulled overly taut. • Route the wire harnesses properly so that they do not contact sharp edges and corners and the end of the bolts and screws on the body. • If a wire harness must contact the end of the bolts or screws or sharp edges and corners, protect the contact part of the harness with a loom or by winding with electrical insulating tape. If the wire harness has a grommet, set the grommet securely. • Take care not to pinch the wire harnesses during installation of a part. If a wire harness has damaged insulation, repair by winding with electrical insulating tape. • When using an electrical tester like a volt/ohm meter or clamp on meter, read the manufacturer’s operating instructions carefully before operating the tester. Be sure that the tester battery is fully charged and the meter is functioning properly
13
2.5 Generator Service Standards Winding Main Winding
Resistance standard (Ω)
Standard value of voltage at No load (V)
0.75-0.85
240
Secondary Winding
2.5
135
Sampling Winding
0.5
16
2.5
13/13
40-45
70
Charge Winding* Rotor Winding
*Charge receptacle removed from North American models but windings are present
14
2.6 Fasteners and Torque Values (1) KDE5000E Item
Inner diameter of
Description
screw X length
Torque Value N.M
Lbf
Front end cover
Hexagonal flange face bolt
M8X25
18
13
Rotor through bolt
Hexagonal flange face bolt
M10X210
50
36
fore/back end cover
Hexagonal flange face bolt
M6X140
10
7
Frame power
Hexagonal flange face bolt
M10X45
40
29
Tighten bolt of
M10
40
29
Earth wire
Hexagonal bolt Hexagonal flange face bolt
M6X12
9
7
Electromagnet
Cross slotted pan head screw
M3X5
Cross slotted pan head screw
M4X8
Anti-hunting bracket
Hexagonal flange face bolt
M8X16
20
15
Oil tank
Hexagonal flange face bolt
M6X25
9
7
M6
9
7
M6X25
9
7
M6
9
7
Hexagonal bolt Decorating plate
Hexagonal flange face bolt Hexagonal bolt
Carbon brush
Hexagonal flange face bolt
M5X20
Rectification block
Hexagonal flange face bolt
M5X20
Earth wire
Hexagonal flange face bolt
M5X12
Back cover
Hexagonal flange face bolt
M5X12
AVR
Hexagonal bolt
Oil tank assembly
Cross slotted pan head screw
M5X12
Cross slotted pan head screw
M5X8
Nut
M6
9
7
Cross slotted pan head screw
M6X16
9
7
regulator
Hexagonal flange face bolt
M6X18
9
7
Battery bracket
Hexagonal flange face bolt
M8X16
20
15
Hexagonal bolt
M8
30
22
Hexagonal flange face bolt
M6X12
9
7
Nnt
M6
9
7
Butterfly nut
M6
9
7
Panel
M5
Hydraulic pressure
Battery
15
(2) KDE5000TA Item
Inner diameter of
Description
screw X length
Torque Value N.m
Lbf
16 tooth bolt
30
22
Hexagonal flange face bolt
M10X225
50
36
front/back end cover
Hexagonal flange face bolt
M6X150
10
7
Frame power
Hexagonal bolt
M8
18
13
Hexagonal bolt
M10
50
36
Earth wire
Hexagonal flange face bolt
M6X8
9
7
Muffler
Hexagonal bolt
M8
30
22
Fixed
Hexagonal flange face bolt
M8X25
20
15
Hexagonal flange face bolt
M6X12
9
7
Cross slotted pan head screw
M6X16
9
7
Nut
M6
9
7
AVR
Hexagonal flange face bolt
M5X16
Carbon brush
Hexagonal flange face bolt
M5X20
Rectification
Hexagonal flange face bolt
M5X20
Earth wire
Hexagonal flange face bolt
M5X12
Back cover of motor
Hexagonal flange face bolt
M5X12
Oil tank
Hexagonal flange face bolt
M6X20
9
7
Fixed air cleaner
Nut
M6
9
7
Charging regulator
Hexagonal flange face bolt
M8X25
20
15
Bracket
Hexagonal flange face bolt
M6X12
9
7
Battery bracket
Hexagonal flange face bolt
M8X16
20
15
Hexagonal bolt
M8
20
15
Hexagonal flange face bolt
M6X12
9
7
Hexagonal bolt
M6
9
7
Butterfly nut
M6
9
7
British standard3/8 Front end cover Rotor through bolt Tighten bolt of
Panel
Battery
16
2.7 Digital Panel Protection Values (1) Low oil pressure protection- oil pressure low for 5s: shutdown and display P-01 (2) Under frequency protection- output frequency = 57 Hz for 10 seconds: shutdown and display P-02 (3) Over frequency protection- output frequency = 65HZ for 10 seconds: shutdown and display P-02 (4) Under voltage protection- output voltage = 105V or 210V: shutdown and display P-03 (5) Over voltage protection- output voltage = 132V or 264V: shutdown and display P-03 (6) Over load protection- output current exceeds 21.2/42.4A: shutdown and display P-04 (7) Charge malfunction warning: no protection but display P-05 (8) High temperature- no protection or fault: water cooled engine models only 2.8 Troubleshooting 2.8.1 General symptoms and possible cause (1) Diesel engine can not start or difficult to start (see engine repair manual) Fault:
Remedy:
Deteriorated diesel oil in fuel oil
Drain the fuel oil, check and clean
Fuel oil is not sufficient
Refill the fuel oil
Fuel cock is not at START position.
Turn it to START position
Fuel delivery line to fuel tank is bent
Check
or pipe is clogged Fuel filter is clogged
Clean or replace
The injection pump does not deliver fuel
Remove the high pressure fuel line, check for fuel flow, repair or replace pump
Fuel injector does not deliver fuel
Remove the fuel injector, check nozzle- clean or replace
The governor lever of engine throttle is not at
Switch on
START position Engine oil filter is clogged causing low oil
Clean or replace
protection Solenoid fuel valve is clogged or does not work
Check the 12V power supply and/or replace
because power is off
solenoid valve
The governor lever of engine throttle is defective
Check and replace as necessary
The ignition switch fails to engage starter
Check battery condition then check switch
Starting motor is defective
Replace
Oil alert switch won’t allow ignition
Check and replace as necessary
The battery has is discharged
Check battery and battery charge regulator
Valves are improperly adjusted
Check or adjust valve clearance.
Engine is seized
Check
and
observe
the
engine
rotation,
disassemble the engine to determine reason for failure.
17
(2) Engine speed is unstable, too high or too low (see engine repair manual) Fault:
Remedy:
The fuel supply is insufficient
Adjust or disassemble to clean
Injection pump or injector is defective
Check or replace
Generator has an overload or short circuit fault
Repair the fault
Engine governor spring is faulty
Repair the fault
Valves out of adjustment
Adjust
(3)The generator produces no AC power or the voltage is abnormal or fluctuating. Fault:
Remedy:
Gauge panel of
1.
generating set
function
Circuit
breaker
fails
to
Remove it and check for open circuit. The resistance reading in multimeter should be “0”
2. The wiring of gauge panel is
Check the wiring harness.
loose 3.
The
connection
of
Check or replace receptacle
receptacle is loose or contact broken. Alternator fault
1. The stator leads are not
Check the wiring harness
properly connected 2.The four point output terminal
Check or replace terminal
is cracked 3. Short, open, or grounded
Check resistance values of all windings.
stator windings
Replace stator is shorted, open or grounded
4 Loss of magnetism in main
Check AVR
rotor 5. Short, open, or grounded
Check resistance values and replace rotor as
rotor windings
necessary
6. Carbon brush assembly
Check resistance value at slip rings. Check
defective
brushes for wear, weak spring tension
7.
Insulation
resistance
of
generator is too low.
Check insulation resistance of stator and rotor. Replace stator and rotor as necessary.
18
(3) AVR fault 1. Voltage can not be regulated
Adjust or replace AVR
2. Generator set automatically stopped after
Check output voltage, adjust or replace AVR
loading, current setting incorrect 3. Electric component failed
Replace AVR
4. Sampling signal but no exciting output
Check exciting output voltage of AVR. Adjust and or replace.
5. The voltage can not be established because
Check that the voltage of main winding is 6 V or
of insufficient residual voltage in the stator
more with AVR disconnected.
6. Power loss is increased because of higher
Check that the voltage of secondary winding should
voltage output of the secondary winding
not greater than 140 VAC
7. The voltage deviation of zero load and full
- Check AVR and stator.
load is too large.
- This may be caused by operating the generator in too high an ambient temperature.
8. Overload shutdown caused by high power
Check inductive loads for low power factor and
factor loading
adjust size of load to rated power*
* Divide the appliance current draw by its power factor to determine the effect on the generator. A device pulling 40 amps with a power factor of .85 places a 47 amp draw on the generator (40/.85). In this example, the generator would experience an overload shutdown. (4) Control panel fault Fault:
Remedy:
1. No display on screen.
- Check 12V power supply of the generator and check
2. Displays wrong code.
wiring .
3. Generator cannot start.
- replace screen
19
2.8.2
Troubleshooting flow charts
(1) Hard starting
20
(2) No AC voltage
21
(3) No Voltage Regulation
22
(4) Generator shutdown
23
3. GENERATOR REPAIR 3.1 Start switch Check: Circuit should be closed when switched on. Circuit should be open when switched off. In starting position the circuit should be closed. 1
2
3
OFF ON
----------
---------
START
----------
----------
----------
.
24
4
5
6
7
---------
----------
----------
----------
3.2
Voltmeter (KGE5000E)
Check generator output with a voltmeter. The reading should agree with the voltmeter. If the voltmeter has no output or it varies with the generator output, test and replace as necessary.
3.3 Circuit Breaker Check: Measure the resistance at two ends of air switch with a multimeter. The resistance should be infinity when the circuit breaker is in the off position and zero when on.
25
3.4
Oil alert PCB and pressure switch
26
27
28
3.5
Generator
3.5.1 Check (1) Front end cover: check for cracks (2)Generator fan: check for missing or chipped blades (3)Rotor: make sure it is clean and free of engine contaminants like grease and oil. Normal measured resistance should comply with section 2.5.
The copper windings
should be clean and bright with no trace of corrosion. Black or cracked windings indicate a short necessitating replacement. (4) Clip ring: It should be smooth without any defect or distortion. The semicircle of the center boss should be clear. In case of distortion replace the clip ring (5) Through bolt: tightening torque is 37-41 Lbf (50-55 N.m). This is essential to ensure the generator won’t be damaged by scrubbing of the rotor and stator. (6) Stator: Check the external enamel covered wire for defects after disassembly and reassembly. Do not contact the copper windings with ground or pieces of sharp metal to prevent scuffing. Stator checks: Check the resistance of the main winding, secondary winding, sampling winding and battery charge winding. The stator must be changed if any resistance reading is outside the parameters. However, insure that there is continuity in the harness before proceeding with a stator change. (a) Main winding: Check resistance on the four position terminal board. You should have
29
0.75 to 0.85 Ω between L1 and L2 and R1 and R2 (b) Secondary or sub winding: Locate the 4 pin connector at the top of the stator. Check the resistance between the two blue green wires. The nominal value is 2.5 Ω. (c) Sampling winding: On the same 4 pin connector, check the resistance between the two yellow wires. The value is 0.5 Ω. (d) Charge winding: Find the 4 pin connector at the top of the stator. There are only two pins. The resistance value should be 2.5 Ω. (7) Carbon brush: There should be no open circuit between lug and pole of the carbon brush and no short circuit between the two poles. Check the brushes for wear. If the brush wear is uneven or the length is less than 0.12 in. (3mm) (8) Rear end cover: check for cracking. 3.5.2 Disassembly (1) Open the rear end cover for open frame generator. Remove the cabinet, cooling plate, left and right side plates, and muffler for TA model. (2) Remove the alternator assembly with the harness. With the TA model, you must remove the induced draft hood to get to the harness. (3) Remove 4xM6x175M bolt from the rear end cover. (4) Remove the stator. (5) Secure the rotor to prevent it from dropping and remove the 10mm flange bolt. (6) Remove the rotor with a puller. 3.5.3
Rotor Installation
Caution: Remove any dust and oil pollution from the crankshaft and rotor. Check the resistance of the new part before installation. 1)
Insert the semicircle clip ring into key groove.
2)
Install the rotor on the crankshaft.
(3) Secure the rotor with a strap wrench and tighten the 10mm flange bolt: tightening torque: 37.5 Lbf (50 N.m) 3.5.4 Stator Installation (1) Before installing a new stator, check the resistance values of the new part. (2) Adjust the spacing between the stator and rotor. • Insert a feeler gauge between the stator winding and the projection of the rotor. • Rotate the rotor one complete revolution. • Secure the flange bolt connecting stator and front end cover. The locking torque is 7.5
30
Lbf (10-13 N.m) • The correct spacing is 0.020+/-0.004 in (0.25 +/- 0.1 mm)
31
4. Electrical Component Illustrations 4.1 Receptacle wiring
32
4.2 AVR Adjustment
33
4-3 Battery Charge Regulator
4.4 Current Transformer
34
35
4-5 Rotor Checking
Note: use the values for the KDA6700TA for both the KDE5000E and KDE5000TA
36
4-6 Stator Test Points CHARGE WINDING PLUG
SECONDARY AND SENSING WINDING PLUG
CARBON BRUSH
L1 L2 R1 R2
37
4-7 Main Stator Winding Check
Note: use the values for the KDA6700TA for both the KDE5000E and KDE5000TA
38
4.8 Stator Secondary Winding and Sampling Winding Check
Note: use the values for the KDA6700TA for both the KDE5000E and KDE5000TA The color of the secondary winding my be blue instead of green
39
4.9 Charge Winding Check
Note: use the values for the KDA6700TA for both the KDE5000E and KDE5000TA 4-10 Carbon brush check
40
5. KDE5000TA DISPLAY PANEL 5.1
Setting
The digital display panel is preset at the factory. If it becomes necessary to replace the panel, it will have to be programmed before installation. (1) Connect the ribbon cable to the new display unit. Be careful not to twist the cable (2) Remove the back cover of the panel. (3)
Press and hold down the Function “FUNC” and turn the ignition switch ON. Wait 5
seconds to enter the program (4) Locate the five position DIP switch board and put the DIP switches in the following position to set the Proper voltage and frequency: 1 2 3 ON
X
OFF
X
4
5
X
X
X
(5) The three position DIP switch board is factory set but make sure the settings are as follows: 1 ON OFF
X
41
2
3
X
X